Precision and versatility are crucial elements in modern manufacturing processes. One technique that embodies these qualities is the use of blowing moulds. Blowing moulds are versatile tools used in various industries to create a wide range of products with precision and efficiency.
Blowing moulds are specialized tools used in blow molding, a manufacturing process that involves the production of hollow plastic or glass objects. These moulds are typically made of high-quality materials, such as steel or aluminum, and are designed to withstand high temperatures and pressures. Blowing moulds play a crucial role in shaping and forming the molten material into the desired product.
There are three main blow molding techniques that utilize blowing moulds: extrusion blow molding, injection blow molding, and stretch blow molding. Each technique has its unique applications and advantages. Extrusion blow molding is commonly used for producing bottles, containers, and tanks. Injection blow molding is ideal for small and intricate products like medical devices or single-serve bottles. Stretch blow molding is used to create PET bottles commonly found in the beverage industry.
Blowing moulds offer manufacturers a high level of versatility due to their ability to produce complex shapes, sizes, and designs. With the advancement in technology, blowing moulds can be customized to meet specific product requirements. They can accommodate intricate details, including logos, embossing, or unique patterns, providing companies with a branding advantage.
The art of precision is evident in blowing moulds' ability to consistently reproduce the desired product. These moulds are engineered to ensure uniform wall thickness, accurate dimensions, and minimal defects. The precise control over the blowing process allows for efficient production cycles and reduces material waste, making it a cost-effective solution for manufacturers.
Blowing moulds find applications across a wide range of industries. In the packaging industry, they are used to manufacture bottles, containers, and jars. Automotive manufacturers utilize
blowing moulds for producing components like fuel tanks, ducts, and air intake systems. The medical field benefits from blowing moulds to create medical devices and drug packaging. Additionally, blowing moulds are employed in the production of household products, toys, and even large-scale industrial equipment.
Advancements in blowing mould technology continue to push the boundaries of what is achievable in manufacturing. Computer-aided design (CAD) and computer-aided manufacturing (CAM) systems have improved the precision and efficiency of mould design and production. The incorporation of sensors and automation has led to better quality control and reduced cycle times. Additionally, the development of eco-friendly materials and processes further enhances the sustainability aspect of blowing mould manufacturing.
The art of precision in manufacturing is brought to life through the versatility of blowing moulds. From creating intricate designs to producing consistent and high-quality products, blowing moulds play a vital role in various industries. As technology continues to advance, blowing moulds are poised to become even more versatile, efficient, and environmentally friendly. By harnessing the potential of blowing moulds, manufacturers can continue to meet the ever-evolving demands of consumers while achieving greater precision and productivity in their production processes.
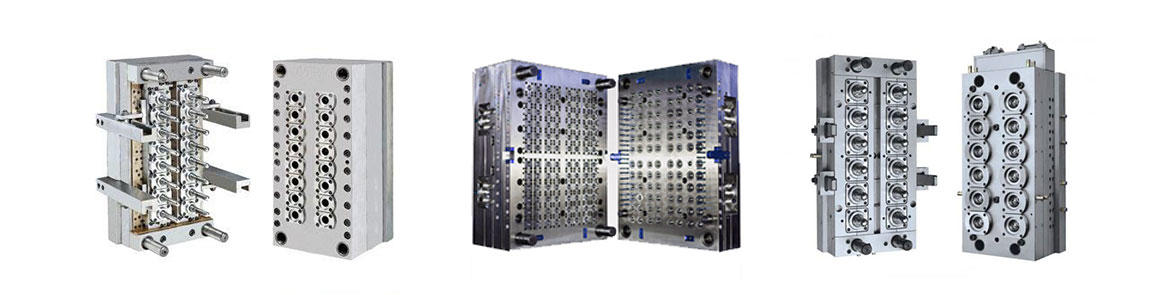